Outcomes & Results
- Delivers and sustains a better performing product
- World-class asset performance thanks to better hand-off communications and higher completion rates
- More accountability across the installation to service handover
- Industry-leading and traceable safety practices
Industry: Vertical Transportation
Size: Enterprise
Location: Global
Use Cases:
- Safety
- Compliance
- Quick quotes
- Installations
- Quality handover
- Safety audits
- Near misses
- Passenger injuries
- Vehicle safety
- Timesheets
- Warrant claims
- Site readiness
Great safety is no accident
Before TrueContext, the organization’s global field teams were fragmented. Every country worked in silos supporting the same ethos of safety first, but without a shared methodology for achieving it. There was no clean way to implement best practices in one country and centralize it across other regions and countries. Process changes also took a longer time to enact and keep pace with ever-changing jurisdictional compliance requirements.
Consistently putting safety first is critical as the vertical transportation industry can be dangerous, whether technicians are building new constructions or maintaining elevators. As elevators are a public transportation system, those working on it and using it in their daily lives need to have the safest asset available. Using near miss data and positive governance allows significant improvements to be made to create a safe working environment and end product.
They achieve that by using TrueContext.
Safety Audits
For inspectors that complete crew safety audits, the enterprise can build sectioned workflows with safety protocols embedded in the form that adapt using conditional logic based on technician input and built-in exception categories. Reference visuals also provide best practices without navigating away from the workflow.
SIF tracking can then be done by branch, including tracking installation, modernization, service and repair employee inspection percentage per quarter sliced by region, district, and branch. This has enabled deficiency counts by safety components.
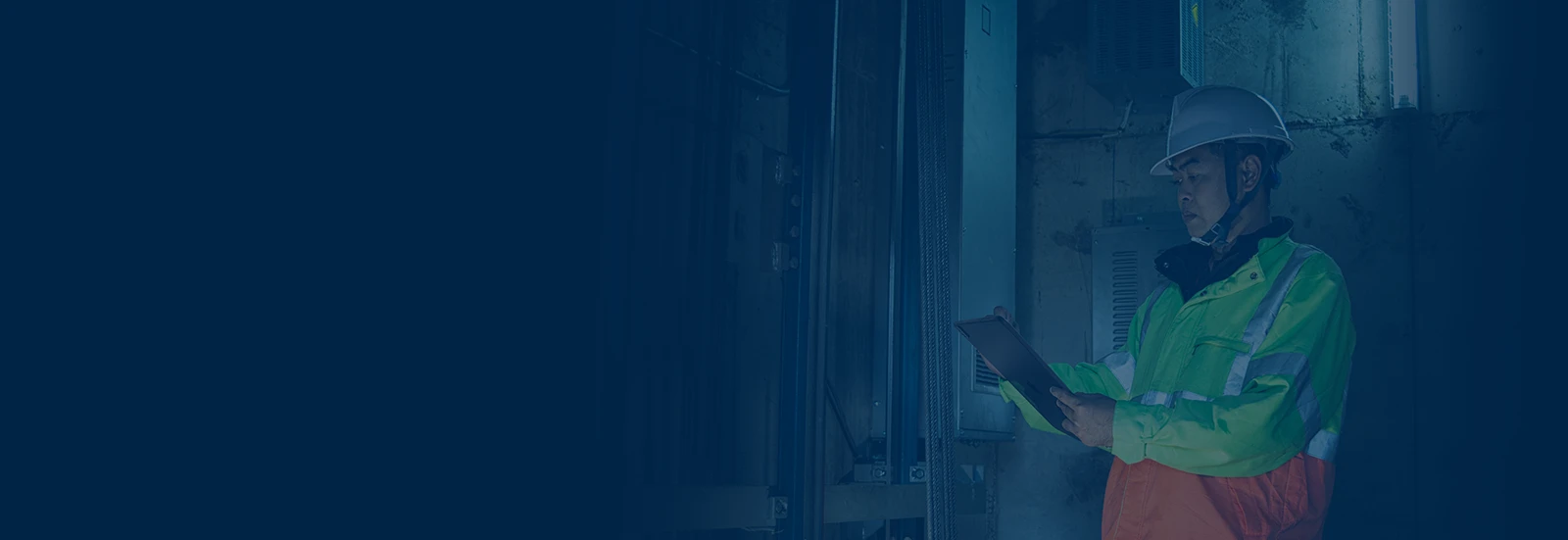
“We were performing thousands and thousands of safety inspections. We were looking to improve the system. The solution – TrueContext.“
QUALITY ENGINEER
Compliance
Working in-compliance is no longer negotiable. Workflows have compliance regulations built into the work technicians complete. This has increased the speed and awareness around open vs. closed directives and reduced fixed costs by limiting costly TSSA follow-ups. Similarly, collected compliance and safety data can be sliced to identify focus areas across 25+ countries.
When regulations change, workflows can be rapidly updated with a few clicks and be reflected across region, district, or branch-without having to manage countless forms based on language. The multi-language feature has allowed the global organization to move from managing forms for every language to having one core form for multiple languages. For an area like Europe this means an easy to roll out a process to different jurisdictions and only one form to manage and iterate-not 10.
This has culminated in being viewed as the best practice in the industry and beyond. When governing bodies like TUV in Germany, Lift Institute, and the Canadian Government are reaching out to the organization as equals and treating them as the gold standard for safety and compliance, it’s clear that no one can tackle, trace, and deliver safety like they can.
Installations that transition seamlessly to service
While safety is embedded into all aspects of the vertical transportation enterprise, the core of their business is the elevators and escalators themselves. When installing an elevator, a supervisor first completes a site readiness form and then hands it to the customer and site team. Site safety checklists and risk and safety audits also happen before the installation of an elevator can begin.
Installation is then completed by a technician with a TrueContext workflow to ensure that the elevator is installed safely and is recorded as in-compliance with regulations. The workflow uses multiple data sources, routes data based on met conditions, and utilizes repeat sections and item entries to speed up form building and asset servicing. During the process, technicians capture photos of the asset that can be data stamped or annotated.
If a technician encounters an issue during these processes, especially for third-party manufactured assets, they can quickly refer to fault codes and gain guidance on how to proceed. Technicians have manuals, troubleshooting guides, and linked data sources that contain all fault codes as well as scripted guidance on procedures that dynamically modify based on each fault code/error. This ultimately saves time on site, allowing technicians to quickly and efficiently complete the job despite technical interruptions.
After the installation is completed, quality audits followed by a final inspection are executed. Finally, the installation is handed over to service in a quality handover form-a critical moment that historically didn’t have the level of visibility required. The enterprise has built a digital installation to service workflow with TrueContext that can track the handover owner at a branch and technician level. It also holds the construction and service teams accountable for delivering the contractual commitment of a quality product that is safe, reliable, and available to customers.
TrueContext supports every step of this process and beyond, ensuring work is completed accurately and safely. All rich data that is collected during this process is fed through analytics, turning it into actionable insights and sliced by completion rates by submission and process monitoring key states.
All this has culminated in a level of excellence and efficiency that the organization can stand on and standardize across all areas of the business that deploy workflows. When organizations like the TSSA see them as an innovator in the areas of asset management, repair, accountability, transparency, and audits-something is being done right in a big way.
New revenue pathways
Despite the incredible impact seen across the organization, this is still only part of the story. Customer satisfaction is an important KPI that workflows have been able to help improve. Not only has improved technician servicing and compliance resulted in higher asset uptime for customers and end users, but there has been a shift to using digital workflows in front of the customer for quick quotes.
Before, a supervisor provided quotes to customers, which resulted in a longer process. The quick quote workflow has allowed technicians directly in front of customers to instantly provide a quote. In fact, 30% more customers sign the presented quote when it is provided by a technician. The more technicians with the ability to quick quote, the more likely new projects, add-ons, and full returns to business are signed.
“TrueContext as a product has the capability to revolutionize how you collect information in the field and use it to jump start internal processes.“
CIO
The story hasn’t finished. The global vertical transportation enterprise’s quest for zero incidents means the need for relentless innovation and process improvement – something that’s only achieved by capturing and tying together data. Compliance regulations change across regions and countries, the needs of customers grow, and process improvement opportunities are there to discover and tighten. They are ready for it.